
Aviation Safety Action Program (ASAP):
[dg ids=”140796,140797″]
FAA Certification Cards
Are you aware that even though Flight Attendants aren’t required to carry their FAA Certification cards, if an FAA inspector is conducting a check ride and requests to see it, you are required to provide your certification number to the FAA within 14 days? The following information was provided by a safety friend from another airline, and we thought it was information that would benefit all of you.
You can obtain a new certification card online (Airmen Online Services Account required) at http://www.faa.gov or you can request the card by mail. You will receive the card much faster if you request one online. If you request the replacement card online it will take around 14 days for you to receive a new card. Should you decide to request a replacement card by mail (in writing) it can take anywhere from 4 to 6 weeks before you receive your replacement.
To request a replacement certificate on-line:
(1) Create an account with Airmen Online Services. Follow the directions found at Airmen Online Services
NOTE: In order to create an account with Airmen Online Services, the flight attendant must know the number of his/her original Certificate of Demonstrated Proficiency. If you do not have your original certificate number you must contact Southwest Airlines in order to obtain that number <or> make your request via mail per the instructions below.
To request a replacement certificate in writing:
(1) Include the following information in the request:
* Name
* Date and place of birth
* Social Security Number (SSN) and/or certificate number, and
* Reason a replacement certificate is required
NOTE: Incomplete information could delay the issuance of a replacement certificate.
(2) Optionally, complete this downloadable form Application for Replacement of Lost, Destroyed or Paper Airmen Certificates to request a replacement certificate.
(3) Include a check or money order for $2, payable to the FAA, when requesting a replacement certificate.
(4) If your permanent mailing address is listed as a Post Office Box (P.O. Box), General Delivery, Rural Route, or Star Route, provide directions or a map to locate your residence.
(5) Mail requests to the following address:
FAA
Airmen Certification Branch, AFS-760
PO Box 25082
Oklahoma City, OK 73125
Aviation Safety Action Program (ASAP) - Improvements
We recently met with the company to discuss our LOU (Letter of Understanding) which addresses the discipline clause attached to the ASAP program. The previous LOU (dated April 1, 2013) gave a member of In-flight management the ability to discipline a Flight Attendant if they witness and reported a Safety event/infraction committed. The Flight Attendant(s) involved could still complete an ASAP report but acceptance of the report did not have any bearing on the ability of Management to issue discipline. Through the discussions with Management, agreement was reached to revise the LOU.
Our new LOU which went into effect March 1, 2014 gives a Flight Attendant 24 hours from their point of knowledge of the Safety event/infraction to complete an ASAP report. If the report is filed within the 24 hours of knowledge and is accepted, no discipline will be issued by the company, even if it is witnessed by a member of In-flight management.
Below you will find a Q & A that addresses these important changes to the ASAP LOU and how it affects the program. For a general Q & A which offers an overview of the program and copy of the LOU, please log into: SWALife->Inflight->Safety on the Fly.
Aviation Safety Action Program (ASAP) - Q&A
Can I be disciplined for filing an ASAP report?
NO – discipline will never be issued for completing an ASAP report
If a Safety infraction is witnessed by a member of Inflight Management, can I receive discipline for the event?
If a safety infraction is witnessed by a member of Inflight Management you have 24 hours from having knowledge of the event to complete an ASAP report. If the ASAP report is accepted then discipline would not be issued. If the ASAP report is not filed within 24 hours of having knowledge of a safety infraction then the Company may issue discipline even if the report is accepted into the ASAP program.
If a Safety infraction occurs and is not witnessed by a member of Inflight Management, but is brought to their attention from another source, can I receive discipline the event?
Once you are made aware of the event, you have 24 hours to complete an ASAP report. If the ASAP report is accepted then discipline would not be issued. If the ASAP report is not filed within 24 hours of having knowledge of a safety infraction then the Company may issue discipline even if the report is accepted into the ASAP program.
If I complete an ASAP report, will the contents of the report be shared with Inflight Management for the purpose of issuing discipline?
NO – any information that is gleaned from an ASAP report will not be shared with the company for the purpose of issuing discipline or to be used in the fact-finding process
Will the information that is submitted in an ASAP report ever be shared with the company?
When an ASAP report is submitted into the program, all the personal information is removed from the report prior to the ERC reviewing the report. If the report is accepted into the program, the unidentified information may be shared with the company to help alleviate and resolve the safety concern
If I inadvertently cause a safety event that the company gains knowledge of, can I complete an ASAP report?
Yes, an ASAP report can be completed anytime a safety event is committed or witnessed.
How could the company gain knowledge of a safety incident that I commit if they do not actually witness it?
There are many ways the company gains their knowledge; they could receive an IR or report from another work group, receive a customer complaint or get a complaint from a fellow co-worker.
If I inadvertently cause a safety event that the company gains knowledge of, can I receive discipline for the event?
If the infraction is not witnessed by a member of Inflight Management, and the report is filed within 24 hours of your knowledge of the event and the report is accepted into the ASAP program, then discipline will not be issued. If the report does not meet the selection criteria for acceptance into ASAP, or the report is not filed within 24 hours and the report is excluded from the program, then the company can process the event through their normal channels. The information that was submitted in the ASAP report is NOT shared with the company to aid in their investigation
If I inadvertently cause a safety event that the company gains knowledge of, can the company investigate the event if I complete an ASAP report?
Yes, if the company receives notification of a safety violation, they will initiate an investigation into the event. The company will share their knowledge of the event with the ASAP ERC to aid the ERC in their investigation. If the report is accepted into the ASAP program, no further action will be taken by the company. If the ASAP ERC excludes the report from the program, the company will be able to proceed with whatever action they deem appropriate.
If I am called into a fact-finding meeting regarding a safety infraction, can I complete an ASAP report at that time?
Once you are notified of the safety infraction, you have 24 hours to complete the ASAP report. The ASAP report would have to be completed 24 hours from the notification of the safety infraction which usually occurs prior to the fact finding meeting. Once the fact-finding meeting starts, you would normally be outside of the 24 hour timeframe. An ASAP report could still be filed and accepted into the program, but you could still be subject to discipline.
Can the Company conduct an investigation into an event they gain knowledge of once an ASAP report is filed?
YES – the company can conduct their own investigation into an event while the ERC is determining if the event meets the acceptance guidelines as outlined in the MOU (Memorandum of Understanding). If the event was filed in the appropriate timeframe and the report is accepted into the ASAP program, then the company will cease its investigation and remove all documentation from the employee’s file.
***If the ASAP report is excluded from the program, the ASAP ERC does not release any information that was gathered through the ASAP process to the Company to aid in their case.
Is the discipline timeframe affected by this process?
If the company is conducting an investigation into an event that an ASAP report has been filed on, disciplinary action will not be taken while the report is being reviewed in the ASAP program. If the report is excluded by the ASAP ERC, the 7 business day timeframe starts on the day the Flight Attendant is notified that the report has been excluded from ASAP.
Why are these changes being made to the ASAP Program?
The Company and the Union periodically review all facets of the ASAP program including the Letter of Understanding (LOU) between the SWA & TWU concerning non-discipline incentives built into the program. The intent of the ASAP program is to identify safety hazards in our workplace and it is the task of the ASAP ERC to try to mitigate these hazards.
Last year upon our LOU review it was determined that the integrity of the program became compromised by the number of reports that were knowingly being submitted as a means to escape discipline, instead of submitting them to help promote safety. This was when the LOU changed and allowed the Company unilateral discretion in issuing discipline on any safety event witnessed and reported by a Member of Inflight Management, regardless of whether the individual filed an ASAP or not.
Upon this year’s LOU review it was determined that this change hindered our ability to identify systemic problems in our operation based solely on who witnessed an infraction which again, is not within the spirit or intent of the program. So TWU and SWA put our heads together and attempted to level the playing field by applying the same acceptance criteria to reported safety transgressions to the Company as those reported to the FAA. This is why we now will apply the 24 hour reporting rule to safety transgressions the Company has knowledge of; the same as we apply to those the FAA has knowledge of. Of course, events that neither the Company nor FAA has knowledge of [reporting time frames] remain unchanged (there is no time frame in these cases).
Q&A Version: v.032014
Health & Safety Reporting
Safety, Incident, or Event Reporting Requiring Follow-up or Response
Aviation Safety Action Program – ASAP Reporting:
What is ASAP? ASAP is an acronym for the Aviation Safety Action Program. This program is a joint effort between Southwest Airlines, TWU Local 556, and the FAA. The intent of this program is to improve the Safety of our operation by offering the chance for Flight Attendants to voluntarily disclose Safety-related events.Flight Attendants who submit a qualifying ASAP report will face no disciplinary action and will receive either no action or only administrative action from the FAA. This is true of reports containing data and information that would not otherwise be known and have been received from an individual Employee through a voluntary report. Additionally, no data or information gathered by the report may be used to initiate, facilitate, or support any FAA legal enforcement or Company discipline except as specifically set forth in the Memorandum of Understanding (MOU). The MOU has been approved by Southwest Airlines, TWU Local 556, and the FAA. A copy of the MOU may be found in the ASAP booklet on SWALife.
The information obtained from ASAP reports will be used to develop corrective action to solve safety issues and eliminate deviations from 14 CFR. Southwest Airlines Leadership is committed to fostering a successful safety culture through ASAP. TWU Local 556 is committed to full support in order to promote membership participation and instill confidence in the partnership process. The Federal Aviation Administration is committed to providing full partnership participation and leadership support in order to maintain the level of trust and cooperation necessary to guarantee the success of ASAP and other voluntary safety information programs.It is through this cooperative effort between Southwest Airlines, TWU Local 556, and the FAA that flight Safety will be improved.
To submit an ASAP report, go to the Inflight Page in SWALife > then simply go to Crew Member Tools > ASAP > launch ASAP. An online tutorial is also available under the Safety on the Fly portal. This tutorial gives a step by step demonstration of how to submit an ASAP report.
General Health and Safety Reporting NOT Requiring Follow-up or Response
The General Safety & Health Incident Reporting Form which is to be used for all incidents on or off the aircraft while on duty except those involving AIR QUALITY on board the aircraft, click below to print a form:
GENERAL SAFETY & HEALTH REPORTING FORM
After downloading and filling out the appropriate form, please scan and email to: mmassoni@twu556.org fax it to: 214-357-9870.
Cabin Air Quality Reporting
The Basics
Crew and passengers regularly report problems with aircraft air quality. Ever noticed that the air in the cabin gets stuffy, and that sometimes the air conditioning is turned off completely on the ground? Ever found the aircraft far too hot or too cold and you are just left to deal with it? Ever noticed that some aircraft have those air nozzles (“gaspers”) over each seat and some don’t? (And that some of them work and some don’t?) Ever found that sometimes you can’t get a deep enough breathe, like there isn’t enough oxygen? That the cabin regularly smells like fuel, deicing fluid, or diesel exhaust before takeoff? That the galley is freezing? Ever smelled heated hydraulic fluid or oil that comes from the air supply vents overhead, or noticed that you seem to regularly get a cold or some other bug after flying? These are documented and routine complaints with aircraft air quality, and are described in more detail on this site.
When you consider that air quality on aircraft is effectively unregulated – unlike almost all other indoor environments – and that there is no government reporting system to systematically collect the data, it’s no big surprise. The airlines and manufacturers can get away with cutting these corners to save money, leaving crew and passengers with symptoms that range from headaches and nausea to fainting and nerve damage. Get informed and submit reports to TWU. Crew and passengers need to unite and speak out to the airlines and the FAA with a strong and united voice.
What You Need To Know
Adapted by: Michael Massoni – from a publication of the Association of Flight Attendants, AFL-CIO
One of the reasons the TWU Safety Team implemented the Aviation Safety-Security and Health Database Incident reporting system (ASHDI) was to track and trend air quality problems our Members are experiencing on the line. This is because some of our Members report health problems that they attribute to breathing poor quality air in the aircraft cabin. Local 556’s Safety Team is and will continue to be active in addressing this industry wide problem. The key to addressing this problem is quite simply: accurate; timely reporting of air quality problems you experience on-line. This will allow us to track, trend and most importantly, act when a qualified incident occurs. Additionally, tracking and trending bad air quality incidents will give us the quantity of data needed to support the argument that there is indeed a problem with air quality on our aircraft. The following Q & A will give you an overview of the 3 basic types of problems with air quality on aircraft and will allow you to better identify if you are experiencing an air quality problem on one of your flights. The intent here is to encourage your reporting of any and all incidents of poor air quality to us via ASAP.
What is the problem?
Our Members report health problems that they attribute to breathing poor quality air in the aircraft cabin. Maybe the air doesn’t have enough oxygen and maybe it is contaminated with cleaning products, de-icing fluid, oil, or pesticides. Exposure to viruses (like the common cold) and bacteria (like tuberculosis) are also reported.
Basically, there can be four major types of problems with the air quality in the aircraft cabin: (1) not enough oxygen; (2) not enough outside air to dilute whatever is in the cabin air; (3) a contaminated air supply.
Problem 1: Not enough oxygen?
The aircraft cabin must be pressurized because there is not enough oxygen in the air above 25,000 feet for you to survive for more than a minute or two. It is important to remember that the amount of oxygen in the air is pretty much independent of the ventilation rate, namely, how many air packs are operating or on what setting. The amount of oxygen available to your body will depend on the altitude to which the cabin is pressurized. For example, the aircraft might be flying at 40,000 feet but the cabin may be pressurized to 8000 feet. Aircraft cabins are not always pressurized to 8000 feet — that is the highest allowable. If a pilot is flying at a lower altitude, then the cabin will likely be pressurized to a lower altitude as well. Flying at a lower altitude likely means that you get more oxygen but it also means that the aircraft uses more fuel.
When it comes to oxygen, you might be told all about partial pressures and percentages, but the bottom line is this: all other things being equal, there is less oxygen in the air when the cabin is pressurized to 8000 feet (for example) than on the ground — about three-quarters as much (74%). If your body is in good working order, you should use that smaller supply of oxygen more efficiently than you would on the ground. For example, a group of rated airline pilots whose blood absorbed about 97% (95-99%) of the maximum possible oxygen on the ground absorbed about 89% (80-91%) at altitude(1).
Remember that Joe Public is not exactly in the same fitness and weight category as a rated pilot, and that smoking, being overweight, being older, not being fit, and taking certain medications will mean that your body will use that smaller amount of oxygen less efficiently.
There are mixed reviews as to whether or not the amount of oxygen you get when the cabin is pressurized to 8000 feet is enough. The Federal Aviation Administration (FAA) set a rule in 1957 that the airlines cannot pressurize the cabin to an altitude higher than 8000 feet. At the time, they did not explain their reasons for choosing 8000 feet as the limit, and the issue has not been revisited since.
Some articles suggest that the 8000-foot limit was developed for the needs of super-fit military types (2) and that a 6000-foot limit would be more appropriate for the rest of us (3). Still, other people say that aircraft could be safely pressurized to an even higher altitude, meaning less oxygen for you.
It is true that people who live at 8000 feet (like in Buena Vista, Colorado) breathe air with this smaller amount of oxygen all the time, but their bodies have had time to adjust (or “acclimate”). Apparently, it takes the average person about six weeks of living at that altitude to properly adjust. Certainly, all other things being equal, you need more oxygen than the passengers do because you are moving and lifting and pushing and carrying, while they are watching a movie or sipping a drink.
In summary, there is less oxygen in the cabin air at altitude than on the ground. It is not clear if this reduced amount of oxygen is appropriate for people with certain physical conditions.
Problem #2: Not enough outside air.
The air inside the aircraft can be contaminated from a variety of sources. Maybe some deicing fluid vapors leaked into the cabin before take off, or the cabin wasn’t ventilated for long enough after pesticides were applied. Upholstery and carpet can emit low-level gases, and can be contaminated with allergens from pet hair that people bring in on their clothes. Damp insulation behind the walls can be a breeding ground for mold, and the insides of the ventilation ducts can be coated with oils.
On top of this, you (and everybody else) are a source of “bioeffluents”; for example, when you breathe out, your breath contains all kinds of gases and vapors (such as carbon dioxide, ethanol, and aldehydes). Water droplets in your breath (or in a sneeze or cough) can transport bacteria or viruses into the air. Meanwhile, you are busy shedding skin particles (that also serve to transport bacteria and viruses) and your digestive system is busy generating gases.
Typically, half of the air in the passenger cabin is re-circulated. You might be told that if that re¬circulated air is first passed through a high-efficiency filter (“HEPA” — generally considered the champagne of filters), and then it will be clean.
You might also hear that, by cleaning the re-circulated air and reducing the supply of dry outside air, your airline is doing you a favor. After all, you are getting “clean” air that isn’t as dry as usual. This is partly true, but not quite right.
First of all, we have been told that the cockpit gets between 50 and 100 cubic feet per minute per person of outside air, or sometimes a mix of outside and re-circulated depending on the aircraft type. That is up to 20 times more than in the passenger cabin – but how often do you hear pilots complaining about dryness?
Second, not all aircraft are equipped with these HEPA filters because filters are not required. Also, filters are only effective if they are regularly inspected and changed. There are no such regulations in place.
Third, keep in mind that even HEPA filters can only trap solid particles; they don’t remove gases (like carbon monoxide and ozone, for example) from the re-circulated air.
Finally, even if the filter is installed properly and changed regularly, you ideally need a ventilation system that is designed so that the flow of the “supply air” will draw contaminants away from your face and towards the filter (“smart air flow”). Also, the outside air needs to be clean, and you need enough of it to dilute or remove contaminants in the cabin air. Some of these contaminants can be a nuisance, but others can be toxic.
It is true is that the outside air at altitude is very dry. The airlines choose not to humidify the air because moisture can cause problems of its own, such as mold growth and ice build-up in the space between the fuselage and the liner panels in the cabin, depending on the temperature. Mold can cause air quality problems and ice can put stress on the aircraft structure and components.
So, given all of these contaminants, what about the amount of outside air that is brought into the cabin? Would it help to use all of the air packs and turn them on full? In the late 1980s, the National Institute for Occupational Safety & Health reviewed approximately 500 indoor air quality investigations in buildings and concluded that inadequate ventilation accounted for 52% of the indoor air quality problems. Remember that this is in buildings not aircraft, but it is an example of the important role that ventilation plays in maintaining the quality of indoor air.
Certainly, the experts on job-related safety and health hazards at the Occupational Safety & Health Administration tell their compliance officers “extensive air monitoring may not be warranted because inadequate introduction and/or distributions of fresh air may be the main problem”(4).
But how much air is enough? You want enough to dilute or remove contaminants. Is there a minimum required air supply to ventilate the passenger cabin? No. The Federal Aviation Administration just says that the passenger cabin must be “suitably ventilated” (14 CFR 121.219). How much air is supplied in the economy section? Probably between 6 and 10 cubic feet per minute of outside air to each person which is about half what is recommended in buildings and “transportation vehicles.”
Some people say that an aircraft is a “unique environment”, so you don’t need as much outside air as in other vehicles or office buildings. We agree that the aircraft is “unique” but if anything, you need more air.
First, if you don’t feel well on a bus, you can open the window or get off at the next stop. Second, people are more likely to travel on an aircraft when sick than on a bus because it can be expensive or impossible to change a flight.
Third, the concentrations of bioeffluents (those gases, vapors, and skin particles that everybody produces) build up more quickly in an aircraft than in a bigger, less-densely populated space like a building. Air quality measurements indicate that you need more ventilation in an aircraft than in an office building or a school to protect against this (5).
In summary, there is no minimum ventilation standard that applies to the passenger cabin, even though contaminant levels can rise more quickly in an aircraft than in a building because an aircraft is a relatively small space.
Problem 3: Contaminated air supply.
The final problem is that sometimes the source of the contamination can be the air supply-itself.
First, if your plane is “sitting in traffic” then the auxiliary power unit (more on that later) or the ground power supply might be sucking in exhaust fumes, including nitrogen dioxide. Also, at altitude, the outside air may contain ozone gas.
In addition to exhaust and ozone, the air supply can be contaminated internally. This problem is not new – it has been recognized by the airline industry for at least 20 years.
How does the ventilation system on airplanes work?
Outside air is usually heated and compressed in one of two places before it is conditioned, mixed with re-circulated air, and then sent to the cabin.
One of those places is the auxiliary power unit (APU), which is an engine that is independent of the aircraft engines. In most cases, it sits in the tail of the aircraft. The APU is often used for air supply on the ground, and on many aircraft types, it supplies the cabin with air during take off and ascent when the aircraft engines need all of their compressed air for engine thrust. In some cases, the APU can be used during other phases of flight.
Moving parts in the APU are lubricated with oil and if the system has been overfilled with oil, or if there is a leaky seal or a cracked joint, for example, then the heated oils or the gases that can be generated when the oils are heated, can leak into the air supply. And it’s not just oil within the APU that can contaminate the air supply; the APU inlet can also cause a problem. The inlet is usually located in the belly of the aircraft at the back and it can act just like a vacuum cleaner hose, sucking in whatever it finds nearby. For example, hydraulic fluids, oils, lavatory water, and deicing fluid that spill or spray into the belly from various locations throughout the aircraft will naturally flow towards the back of the aircraft when the aircraft is moving forward. If the APU is operating, those liquids can get sucked into the inlet valve and then mixed into the air that is then supplied to the cabin and cockpit.
The most likely place for the outside air to be compressed is the aircraft engines. Most of the air compressed in the aircraft engines is used for engine thrust, but a portion of that compressed air is routed to the ventilation systems.
Like the APU, the aircraft engines are full of moving parts that are lubricated with oils — oils that can leak into the air supply. In addition, the air compressors in wing-mounted engines can ingest hydraulic fluids from local hydraulic systems if there is a line break, for example. And finally, just like the APU, the air compressors in tail-mounted engines are like a vacuum cleaner hose and can suck in fluids that may have found their way into the belly of the aircraft.
Can we prove that this happens?
Leaks and spills of oils and other fluids are reported infrequently but persistently. In some cases, it has been possible to confirm symptom reports with airline mechanical records that indicated a leakage or a problem in the APU or engines. Airline mechanical records should be freely available to affected flight attendants, but in fact, they are very difficult to access. The best way to prove that a mechanical problem resulted in a contaminated air supply is to monitor the air supply during an incident, but this has been challenging, partly because of the costs involved. Even though the airlines are not required to monitor the air supply, the FAA has formally acknowledged that the air supply, at least on certain aircraft types, can get contaminated in this way. On 8 August 2000, they published an Airworthiness Directive that requires certain modifications to the hydraulic lines and related parts in the APUs of certain McDonnell Douglas aircraft types. The directive was “prompted by reports of smoke and odor in the passenger cabin and cockpit due to hydraulic fluid leaking into the APU inlet, and subsequently, into the air conditioning system” (65 FR 48368, August 8, 2000). This is a step in the right direction but will only address a very small piece of the problem.
What is in the air?
There are two contaminants that raise particular concern: (1) tricresylphosphates (TCPs) which are used as an additive in some popular engine oils; and (2) carbon monoxide, which is a colorless gas that can be formed when you burn oils and hydraulic fluids to high temperatures. TCPs are neurotoxin, which means that they can damage your brain and nerves (6). Carbon monoxide is an asphyxiant – it reduces your body’s oxygen supply. Remember that you are already getting less oxygen when you are in a pressurized cabin than you would on the ground. Other possible contaminants in aircraft air include nitrous oxides and ozone. Both will irritate your throat and lungs.
You might be told that it isn’t possible to be exposed to TCPs or carbon monoxide. Not true! Scientists have heated two popular engine oils to the temperatures found in an operating aircraft engine and found both TCPs and carbon monoxide in the aerosol/fume that was given off (7). So — we know that these contaminants can get into the air supply (because the industry and the FAA say so) and we know what at least some of those contaminants are. We also have reports from hundreds of flight attendants (in the United States, Australia, Canada, Denmark, France, Sweden, and the UK, for example) who report symptoms that are consistent with exposure to neurotoxins (such as muscle tremors, memory loss) and/or asphyxiants (such as headaches, dizziness, nausea). Serious stuff.
To sum up…
Problems with aircraft quality include: (1) not enough oxygen; (2) not enough outside air to dilute or flush out contaminants generated inside the cabin; and (3) a contaminated air supply. Health effects caused by any combination of these problems have not been properly investigated.
You might be told that you have a headache and feel dizzy because you are stressed out, tired, dehydrated, or overweight. Even if you are all of the above, don’t forget about the potential problems and health effects associated with cabin air quality. Some symptoms are a nuisance others are serious.
There are solutions…
To keep you informed, here are some of our recommendations for the researchers, the regulators, and the airlines.
First, we recommend that the justification for the FAA cabin altitude limit is reviewed and that oxygen data be collected from members of the flying public and from flight attendants to examine whether a representative range of people are getting enough oxygen at altitude.
Second, we recommend that the airlines be required to continuously monitor levels of some airborne contaminants during flights. This would help to define what the contaminant levels are, what the ventilation rates are, and what is acceptable.
Finally, the air supply needs to be clean. Long-term activities should focus on changing the design of the ventilation system to reduce the chances of the air from getting contaminated in the first place. Short-term activities should focus on installing design modifications and ensuring regular mechanical inspection, including parts replacement and maintenance, and monitoring the supply air. If airlines routed their aircraft to maximize ground time at maintenance bases, more frequent checks would be easier to achieve.
Whatever the problem, get smart: the passenger cabin is your workplace.
If you have a problem report it the Local 556 Safety Team:
Don’t just accept a headache after every shift. If you need to, make a stink. LET’S CLEAR THE AIR.
Endnotes
(1) Cottrell, JJ; Lebovitz, BL; Fennell, RG; and Kohn, GM. “Inflight arterial saturation: continuous monitoring by pulse oximetry.” Aviation Space & Environmental Medicine, 66: 126-130 (1995). Back
(2) McFarland, RA; Edwards, HT. “The effects of prolonged exposures at altitudes of 8,000 to 12,000 feet during trans-Pacific flights.” Journal of Aviation Medicine, 8: 156-177 (1937). Back
(3) Ernsting, J. The 10th Annual Harry G. Armstrong Lecture: Prevention of hypoxia-acceptable comprimises.” Aviation Space & Environmental Medicine, 49: 495-502 (1978). Back
(4) OSHA Technical Manual, Section III, Chapter 2: “Indoor Air Quality Investigation.” Published by OSHA’s Office of Science & Technology. Occupational Safety & Health Administration, Department of Labor, Washington, DC. January 20, 1999. Back
(5) Walkinshaw, D. “Investigating the impacts of occupancy density and ventilation on indoor air quality of offices, classrooms, and aircraft.” Indoor Air Technologies Inc. (November 2000). Back
(6) Casarett & Doul’s Toxicology. 5th Ed. Eds: Casarett, LJ; Amdur, MO; Klaassen, CD. McGraw Hill, 1995. Back
(7) Van Netten, C. and Leung, V. “Comparison of the constituents of two jet engine lubricating oils and their volatile pyrolytic degradation products.” Applied Occupational & Environmental Hygiene Journal, Vol. 15(3): 277-283 (2000).
Some extra reading
Hocking, MB. “Passenger aircraft cabin air quality: trends, effects, societal costs, proposals.” Chemosphere, 41: 603-615 (2000). National Academy of Sciences/National Research Council “The Airliner Cabin Environment. Air Quality and Safety.” Committee on Airliner Cabin Air Quality. National Academy Press, Washington, DC (1986). Parliament of the Commonwealth of Australia. “Air Safety and Cabin Air Quality in the BAe146 Aircraft.”(Adobe PDF) Prepared by the Senate Rural and Regional Affairs and Transport Legislation Committee. Parliament House, Canberra, Australia. Under October 12, see (October 2000). Seppanen, OA; Fisk, WJ; and Mendell, MJ. “Association of ventilation rates and CO2 concentrations with health and other responses in commercial buildings.” Indoor Air, 9: 226-252 (1999). Springston, J. Abstract presented at the American Industrial Hygiene Conference & Exhibition, Orlando, FL (May 2000). United States Air Force MIL-E-87145 (USAF) “Appendix B. Respiratory Environmental Thresholds and Physiologic Limitations.”
Incident FAQ
IF I AM EXPOSED TO AIR THAT IS CONTAMINATED WITH ENGINE OIL OR HYDRAULIC FLUID ON THE AIRCRAFT, WILL I SEE OR SMELL A SMOKE OR MIST IN THE CABIN?
The short answer is “probably, but not necessarily.” Many crewmembers that have reported air quality incidents to TWU and other unions describe an odorous smoke or mist in the cabin. They might see a fine smoke that smells like burning oil, for example. Or they might see a bluish haze that smells like dirty socks. In some cases, crewmembers do not remember seeing or smelling anything unusual during a flight, although they report symptoms consistent with exposure to carbon monoxide gas or neurotoxic chemicals, and mechanical records confirm that the air supply was contaminated.
WHAT CHEMICALS MIGHT I BE EXPOSED TO AND WHAT ARE THE SYMPTOMS?
You are exposed to a complex mixture of chemicals, although chemical analyses of these fumes have been published. The health effects associated with exposure are not fully known and will vary between people. However, two chemicals of concern are:
a) Carbon monoxide
Carbon monoxide can be generated when oils and hydraulic fluids are heated to high temperatures. Carbon monoxide is a colorless and odorless gas. Although it is possible to be exposed without knowing it, it is unlikely because carbon monoxide is often accompanied by odorous fumes. Carbon monoxide robs your body of necessary oxygen. This is especially problematic during a flight because the supply of oxygen is already reduced, relative to what is in the air you breathe when on the ground. People who smoke already have some carbon monoxide in their blood and therefore have an even lower tolerance for environmental exposure. Also, increased temperature, humidity, and activity level can accelerate the toxic effects of carbon monoxide. The symptoms typically associated with exposure to carbon monoxide are listed in Table 1. This list may not be exhaustive. Also, there will be some individual differences in the way that people react. In severe cases, carbon monoxide can cause long-term or even permanent brain damage, including personality changes, deficits in memory and other thought processes, and symptoms of Parkinson’s Disease. CT and MRI scans may show changes in the brain.
Table 1. Symptoms typically associated with light, moderate, and heavy exposure to carbon monoxide. |
||
Light exposure
|
Moderate exposure
|
Heavy exposure
|
difficulty concentrating headache fatigue nausea |
abdominal pain abnormal heart beat bluish lips and nails chest pain |
balance problems bizarre behavior coma convulsions |
b) Tricresylphosphates
Many oils and hydraulic fluids currently used in the airline industry contain chemicals called tricresylphosphates (TCPs). If the exposure is serious enough, TCPs can damage your brain and nerves. There are many different types of TCPs, and some are more toxic than others. We do not have complete information on the types and quantities of TCPs in the products used on aircraft. Some key symptoms associated with exposure to TCPs are listed in Table 2; all are serious, some more than others. It is important to know that some of these symptoms may not develop right away; instead, they may take weeks to develop.
Table 2. Symptoms typically associated with exposure to TCPs. | ||
Less serious
|
More serious
|
Most serious
|
eye irritation diarrhea gastrointestinal upset headache loss of appetite respiratory tract irritation skin irritation sore, aching muscles |
disturbed sleep excitability/irritability gastrointestinal pain muscular pain, cramps muscle weakness (esp. arms, legs) respiratory tract burning restlessness vertigo vomiting |
abnormal reflexes balance problems convulsions coordination problems delirium depression digestive system damage foot drop memory loss muscle twitching, spasms nerve damage paralysis (esp. arms, legs) stupor tingling, numbness |
Sources of information include International Chemical Safety Cards (published jointly by the International Labor Organization and World Health Organization) and Medline Plus Medical Encyclopedia (published by the US National Library of Medicine and the National Institutes of Health). Also, see following references:
Abelson, A; Sanborn, M; Jessiman, B; and Weir, E. “Identifying and managing adverse environmental health effects: carbon monoxide poisoning” Canadian Medical Association J, 166(13) (25 June 2002).
Parkinson, RB; Hopkins, RO; Cleavinger, HB; et al. “White matter hyperintensities and neuropsychological outcome following carbon monoxide poisoning.” Neurology, 58(1): 35-32 (May 2002).
US Congress Office of Technology Assessment “Neurotoxicity: Identifying and Controlling Poisons of the Nervous System. Chapter 3: Fundamentals of Neurotoxicology – Effects of toxic substances on the nervous system” NTIS order #PB90-252511 (April 1990).
United States Department of Defense “Aeromedical Traning for Flight Personnel: Chapter 5: Toxic Hazards in Aviation” Field Manual No. 3-04.3.01, US Army Headquarters. Washington, DC (29 September 2000).
Oil Fumes - Knowing When Present & Preventing Additional Exposure
Engine oil fumes can contaminate the cabin and flight deck air supply systems on all aircraft types. It is very important to limit your exposure because the fumes are highly toxic and can cause both acute and chronic health problems.
This is what you need to know:
- If oil fumes contaminate the cabin air supply, you may smell and see fumes, or you may not.
- If you do smell fumes, they won’t necessarily smell like oil. Many people think they smell like dirty socks. Others say “chemicals,” “old cheese,” “wet dog,” “heated garbage,” and so on. Boeing has reported that BP2197 engine oil fumes have a characteristic “electrical smell,” often mistaken for electrical faults.
- If you smell what could be oil fumes and are already onboard, quickly verify that nobody is cooking anything smelly, that the coffee pots are not burning, that the cabin lights are working and not burned out, and that the galley chiller lights are not indicating malfunction (red).
- Tell the flight deck that it appears that engine oil has contaminated the supply air. Describe anything you see/smell, plus any symptoms, and report that you have ruled out other sources in the cabin (if applicable).
- If fumes are present prior to pushback, ask the flight deck to have maintenance check the aircraft prior to dispatch. If fumes are present during taxi, make sure the flight deck knows. If fumes are present inflight, ask the flight deck to ensure that maintenance checks the aircraft immediately upon landing. (The pilots may initiate a diversion or return to base.)
Tell The Pilots
SICK FROM POOR AIRCRAFT AIR QUALITY?
TELL THE PILOT. REPORT TO THE COMPANY. REPORT TO NASA. CALL TWU FOR HELP.
It is critical that you tell the Captain if you think there is anything wrong with the aircraft air quality so that it gets recorded in the aircraft log book. Make sure you tell the Captain what you observe/sense is wrong with the aircraft(e.g., smoke, odor, something is not right) and not just your symptoms. The Captain needs and must have aircraft information to make a logbook entry. If the Captain does not write up the aircraft problem then maintenance need not investigate, the airline need not report to the FAA, the problem won’t get fixed, and you have no hard evidence that there was a problem.
Telling the pilot is important but it is not enough. You also need to report to company in writing. File an irregularity report (IR)!
If necessary, fill out an injury/illness/OJI report and ask for a workers’ compensation claim number.
If you are willing, it is beneficial to report these events to a confidential, online reporting system maintained by NASA called the Aviation Safety Reporting System (ASRS). Go to https://asrs.arc.nasa.gov NASA will remove any identifying information (including your airline and the day of the incident) before adding your report to its online database, but it is important for NASA to know about these events because it means that the incident is now documented with an government agency and if everyone reported, there would be enough de-identified reports out there to push Congress to make the FAA act.
PROTECT YOURSELF: if there is a problem with air quality, tell the Captain, file a report with the company to document the cabin conditions, ideally report it to NASA, and call TWU for help.
Sick From Poor Air Quality Checklist
Call TWU and ask them to open a case file with the date, flight #, aircraft #, your symptoms, and any details concerning the event and route the information to Michael Massoni.
TWU will provide you with information and support and will request the aircraft maintenance records on your behalf. These records may help to show whether engine oil or other chemical contaminants entered the cabin air supply.
File an irregularity report (IR) with the company immediately and keep a copy for your records.
File an ASAP report.
If you need medical attention, call your airline to get a workers’ comp claim number so that your medical bills can be processed through workers’ comp. This is important because your regular medical insurance won’t pay for work-related illness or injury and you don’t want to get stuck with the bills.
Get medical attention (as needed) to document your symptoms ASAP.
TWU will fax/email information to your doctor/hospital/you on what you were likely exposed to and what medical tests may be helpful for your first visit. If you want more information for your doc or if you have questions about medical care, call TWU’s Michael Massoni (214-640-4375).
Tell your doctor that you were likely exposed to heated aircraft engine oil or hydraulic fluid that contaminated the air supply system. Give the name of the product and the data sheet. If you don’t know, ask TWU.
Tell your doctor that most engine oils and some hydraulic fluids contain toxic tricresylphosphates (TCPs) and that when the products are heated, carbon monoxide gas can also be supplied to the cabin.
File a WC claim if necessary and keep a copy for your records.
Keep a record of your symptoms in a journal and go to the doctor as necessary so that everything is documented. (You may develop new symptoms for weeks after your air quality event).
Take photos/video of any visible symptoms (rash, tremors, etc).
File a confidential report with NASA online at https://asrs.arc.nasa.gov
Sick From Poor Air Quality Details
REPORT IT – EVEN IF YOU THINK YOU’LL BE BETTER SOON, AND CALL TWU FOR HELP.
If you feel that you may be suffering from symptoms due to exposure to airborne chemicals that were supplied to the aircraft cabin via the air supply system, the best thing you can do for yourself is document it. Don’t just figure you’ll likely feel better soon so there is no need to report anything. If your health problems persist or return after another incident, the paper trail will be critical. Start by calling your TWU Local 556 Safety Team.
If the air supply system was contaminated with heated oil or hydraulic fluid, you might have noticed an odorous smoke, mist, or haze in the cabin. It might have smelled like burning oil or dirty socks. In some cases, crewmembers do not remember seeing or smelling anything unusual during a flight, although they report symptoms consistent with exposure to carbon monoxide gas or neurotoxic chemicals, and mechanical records confirm one or more failures that caused oil or hydraulic fluid to enter the air supply. Many symptoms that you may experience are not specific to contaminated bleed air. For example, you may have difficulty breathing due to insufficient oxygen or exposure to ozone.
If you have symptoms that are visible, have somebody take photos or video as soon as possible. Your doctor is unlikely to do this and it will help to establish the cause-effect relationship that you want to prove. Symptoms such as stomach cramping, fatigue, muscle pain, and confusion cannot be photographed, but must be documented by a doctor. Video may also help.
It is very important that you see a doctor as soon as possible to document your symptoms. Do not just go home. Get medical attention. It is especially important to have everything documented to protect yourself if your symptoms get worse. We have heard from flight attendants who have seen a doctor for bleed air-related complaints and been sent home with antibiotics. This is unacceptable! If you think that you were exposed to heated oil or hydraulic fluids on board the aircraft, you need to tell your doctor. Tell them when and what symptoms you had during the flight, what symptoms developed after the flight, and what symptoms you have now. Describe the conditions in the cabin. Give them a copy of the information on the TWU website (www.twu556.org under About Us: “Health & Safety”), especially TWU’s “What You Need To Tell Your Doctor” bulletin. Call your TWU Safety Team for more information.
Whenever possible, have your doctor perform objective tests to document your condition. For example, if you have respiratory complaints, you might be able to have a lung function test to document any reduced breathing capacity. Nerve conduction velocity tests may be used to confirm nerve damage. If you are dizzy or faint, you may have been exposed to carbon monoxide and a blood oxygen hemoglobin test may be appropriate, although blood must be drawn within a few hours of exposure and within one hour of exposure if you went on oxygen during the flight. Also, you don’t have to be exposed to carbon monoxide to be exposed to toxic oils or hydraulic fluids.
File a report with the company promptly. Note the date, flight number and aircraft tail number. Describe the working conditions. Did you notice an odor or visible mist/haze/smoke? Were you aware of any mechanical problems? During what phase of flight did you develop symptoms? Was this the first time? Send a copy to TWU. TWU will request a copy of relevant aircraft mechanical records on your behalf. These records will help prove that the air supply system was contaminated.
Keep a copy of everything – every medical record, report, and photo. Keep a record of all phone conversations – names, dates, and a short summary of the conversation. If you have to mail anything, send it by certified mail with a return receipt. Reporting to the company is a priority, but to advocate on your behalf, TWU also needs your information. Please contact your TWU Safety Team at mmassoni@twu556.org or call 214-640-4375.
What to Tell Your Doctor
If you believe that you inhaled heated engine oil or hydraulic fluid that entered the aircraft cabin via the aircraft air supply system during your flight, make sure you tell your doctor. Your assessment can be based on: (1) The conditions that you observed in the cabin during the flight (possible odor and/or visible fume/mist); (2) The symptoms that you developed during and after the flight; and (3) In some cases, what airline management or mechanics may have told you about the aircraft.
Your union will request a copy of the aircraft mechanical records that can provide a record of aircraft air supply contamination.These can be useful exposure records for your doctor, but it can take many months to obtain them.
It is important for your doctor to know that heated engine oil/hydraulic fluid can enter the aircraft air supply system, exposing you to a mist or fume that contains a complex and largely unknown mixture of chemicals. The mist or fume can irritate and burn your eyes, nose, and throat. Different airlines use different engine oils and hydraulic fluids. For information on the specific product you were exposed to, get the Material Safety Data Sheet (MSDS) TWU 556 Safety Team (see below) and give it to your doctor. However, make sure your doctor understands that the MSDS typically does not describe health hazards associated with inhaling these products (as they should, because that is how you are exposed to them on aircraft), only drinking them or getting them on your skin, so the health hazard warnings on the MSDS are generally underestimated and incomplete.
Tricresylphosphates (TCPs) are one of the toxic ingredients in engine oils and some hydraulic fluids. Exposure to TCPs has long been associated with initial symptoms of stomach cramps, muscle weakness, flu-like symptoms, and delayed problems with gait, balance, and tingling/numbness. More recent medical papers suggest that even very low levels of TCP can cause chronic symptoms of neurotoxicity such as problems with fatigue, memory, concentration, and speech. These symptoms can develop over days or weeks. A complete list of associated symptoms is attached to this bulletin.
Tell your doctor it is not worth testing the level of red blood cell cholinesterase (also called “acetyl cholinesterase”) because it is a poor indicator of TCP exposure.
Ask your doctor to test the level of plasma cholinesterase (PChe; also called “serum cholinesterase” or “butyl cholinesterase”) in your blood. TCP exposure can cause an initial depression in PChe followed by a “rebound effect.” Multiple measurements over time and careful interpretation of the test results are necessary. Make sure your doctor knows that there are documented reasons why some people have depressed levels of PChe to begin with, putting them more at risk of toxic effects during an incident. For example, menstruation, pregnancy, specific medical conditions (like lymphoma) have been associated with reduced PChe.
Consider a blood test that will tell you if you have a genetic predisposition to elevated risk of toxic effects of exposure as a result of having the defective forms of PChe that are less effective at metabolizing toxins like TCPs. Insurance may not cover this test and even if you do not have the faulty form of PChe, TCPs can still make you very sick. However, a positive result would support your case if you have TCP-related symptoms. The name of the test is dibucaine number (see www.labcorp.com), although it is not widely available.
You can also be exposed to carbon monoxide (CO) gas during these events because oil and hydraulic fluid in the air supply system get heated to high temperatures.
Make sure your doctor knows that it is unlikely that you will get your blood analyzed in time for this test to be useful. “Carboxyhemoglobin” levels in the blood will likely normalize within a few hours after an exposure and even faster if you went on oxygen during the flight (which TWU recommends). The effects of exposure to CO are more intense in-flight than on the ground because you are in a reduced oxygen environment. Even though CO clears from your body relatively quickly, it can still cause a variety of short or long-term symptoms such as dizziness, headaches, and fatigue caused by the exposure so it is important for your doctor to know about it.
Because there is no perfect blood test to prove either exposure yet, many crew and passengers have to rely on medical tests that show damage to your body. The doctor can then decide whether or not your test results are “consistent with exposure to a heated mist of engine oil or hydraulic fluid.” For example:
If you have breathing problems, a doctor can examine your respiratory system and perform lung function tests.
If you have memory or concentration problems, a neuropsychologist can have you take specific tests, both to assess and document any problems and to suggest therapy.
If you have tremors, muscle twitches, or other movement disorders, a neurologist can assess and document the problems, possibly with some combination of a physical exam and a brain scan. Autonomic nervous system testing may also be helpful. Contact the TWU 556 Safety Team for more information.
If you suffer from depression or anxiety after an event, (whether due to brain damage from the chemicals or simply as a reaction to being ill), a psychiatrist can assess your symptoms and help you to manage them, possibly with some combination of therapy and medication.
As general advice, keep a journal of any symptoms you develop. For any visible symptoms (such as a rash or tremor), have someone take a video or photograph. See a doctor as soon as possible to make sure that there is an official record. Keep a copy of all documents and keep a record and short summary of every related phone call.
Download Forms
The Air Quality Reporting Form that is to be used for all on duty incidents involving air quality onboard the aircraft including problems related to pesticide exposure on aircraft; click below to print a form:
AIRCRAFT AIR QUALITY REPORTING FORM
After downloading and filling out the appropriate form, please scan and email to: mmassoni@twu556.org fax it to: 214-357-9870.
Safety Team
The mission of the Safety Team is to provide Union Leadership in all issues of health, safety and security; technical counsel to the TWU Executive Board; representation to our Membership; stewardship within our Company, industry, and its regulatory bodies and most importantly, promote effective communications between all.
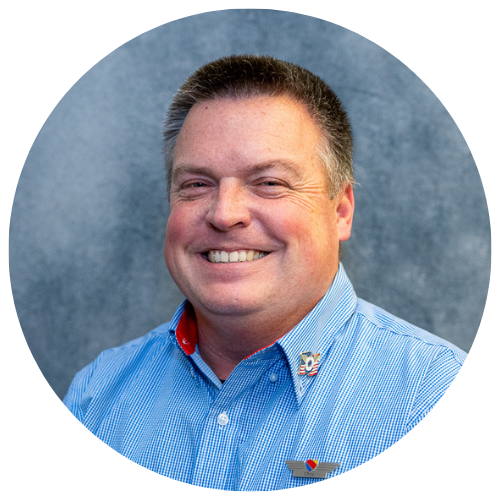
Chris Click
Safety Committee Chairperson - Baltimore-based Flight Attendant
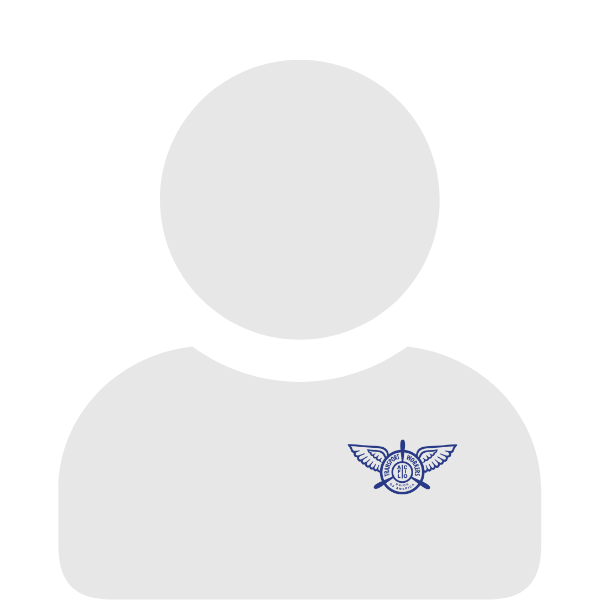
James Jenkins
Safety Committee Vice-Chairperson - Denver-based Flight Attendant
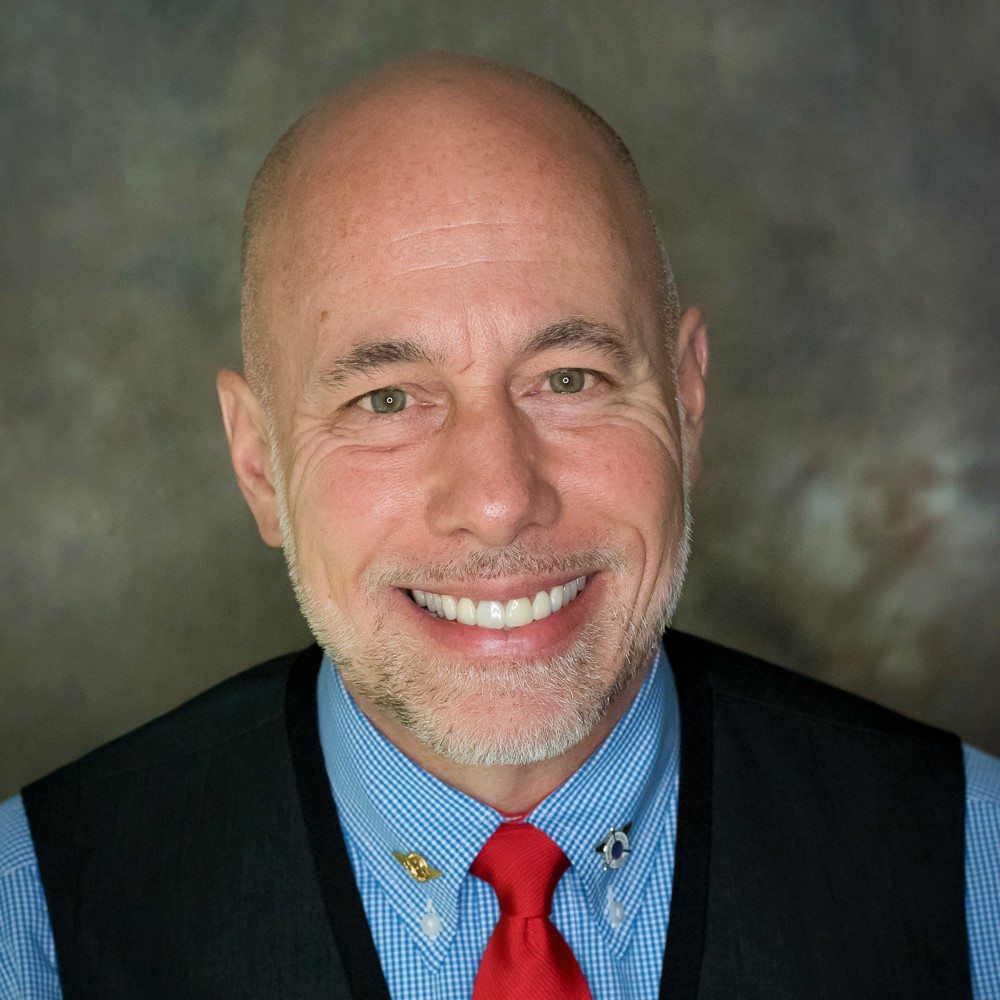
Michael Massoni
Safety Committee Team Member - Phoenix-based Flight Attendant

Michele Moore
Safety Committee Team Member - Dallas-based Flight Attendant

Jannah Dalak
Safety Committee Team Member - Houston-based Flight Attendant

Denny Sebesta
Go Team Member - Dallas-based Flight Attendant